Aluminum, copper, and magnesium make up the majority of the 2024 aluminum alloy’s ingredients. In descending order of quantity, other components which are metallic in nature include iron, silicon, etc. Moreover, it is referred to be one of the most often used alloy having increased strength. Higher purity variant alloys, such as 2124 and 2324, provide stronger materials.
2024 alloy has a high strength-to-weight ratio and a moderately strong fatigue resistance. Although it can be machined to a high degree of polish, it should only be welded in one of three forms: spot, seam, or flash. Due to its copper component, 2024 has fairly low corrosion resistance. Due to this, its usage is frequent in combination with an anodized finish or covered using highly purified aluminum, albeit doing so may weaken the material’s fatigue resistance.
High-strength applications are ideally suited for 2024 extruded aluminum. It is frequently employed in fittings that need to be stiff, strong, and fatigue resistant. Alclad sheet materials are widely used in applications that are used commercially.
Mechanical Properties
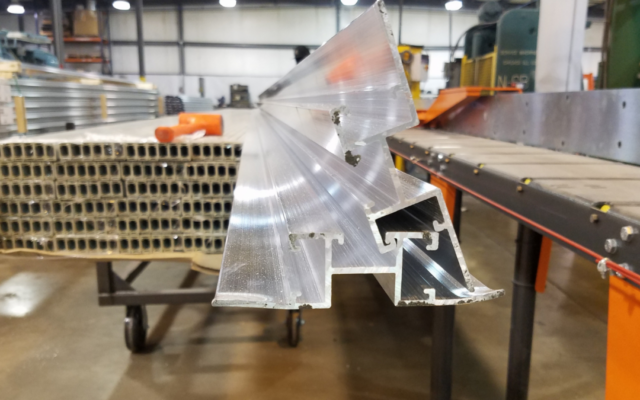
It is possible to identify an aluminum alloy using a few mechanical characteristics. Some critical parameters regarding 2024 aluminum are different strengths comprising ultimate, yield, shear, etc., along with modulus of elasticity. These characteristics will provide a general understanding of a workability of a specific material along with its probable usages.
The highest amount of stress that will cause an alloy specimen to deform either temporarily or permanently is known as the yield and ultimate strengths, respectively. They are crucial if an alloy is being used in static applications like buildings or safety gear, where permanent deformation is not expected to happen. High-strength structural materials like aluminum tubing are attracted to 2024 aluminum due to its exceptionally enormous ultimate and yield strengths of 469 MPa (68,000 psi) and 324 MPa (47,000 psi), respectively.
In addition to structural elements, 2024 is frequently used for various items comprising couplings, fuses, gears, shafts, bolts, etc. This alloy hardens over time and takes heat treatment effectively. Because of its bright surface, alloy 2024-T3 is very useful for repairing and restoring RVs.
The mechanical characteristics of 2024 aluminum can vary significantly depending on its temper. The tempers 2024-O, 2024-T3, 2024-T4, 2024-T6, 2024-T351, and 2024-T851 are the most often used. When 2024 alloy is created in these tempers, some improvements are observed, particularly in the form of enhanced tensile strength. A lot of tempers also offer great deep drilling properties.
Advantages of using aluminum 2024
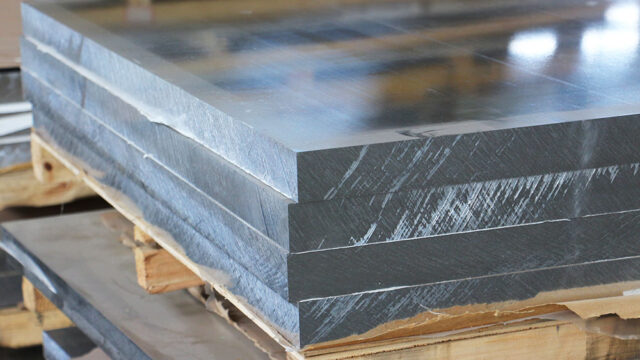
The alloying component in aluminum alloy 2024 is copper. This alloying component provides 2024 more durability and resilience to fatigue. The alloy’s characteristics enable it to sustain significant stress and strain for extended periods. The material 2024 offers the qualities that make it perfect for cylinders blocks, constructions, hardware, truck wheels, and other transportation-related parts and fittings, in addition to having a high yield strength. For several military and aviation applications that involve extremely high temperatures in the engine areas, an aluminum 2024 sheet is the best option.
Increase in strength using 2024 heat treatment
Different aluminum alloys in the 2xxx, 6xxx, and 7xxx series, including 2024, can undergo heat treatment operations. The alloy is heated to a predetermined temperature during the heat treatment process for blending the alloy constituents or homogenizing with the base metal. The metal is next subjected to solution heat treatment for maintaining the components intact.
Copper and other elemental atoms precipitate out of the solution when the object cools. The alloy ages during this process, gaining strength. The designations 2024-T351, 2024-T4, and 2024-T851 may be given to the 2024 aluminum depending on the actual heat treatment and the aging process.
Aircraft industry
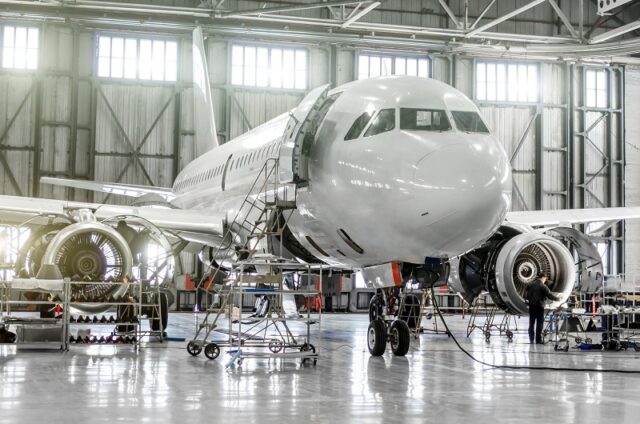
Due to its high strength characteristics, 2024 aluminum extrusion and 2024 aluminum panel are frequently used in aerospace sector applications. However, this alloy also exhibits a comparatively low corrosion resistance. It is frequently covered in aluminum or Al-1Zn for protection when utilized in aviation sheet applications, which may reduce its fatigue strength.
Although its capacity to resist corrosion is dubious, it has good machinability properties. These characteristics are essential for applications that call for machined parts and precise fitment. The excellent grain structure of the alloy makes aluminum 2024 perfect for applications requiring cold heading and thread rolling. Copper serves as the primary alloying component in 2024 aluminum. This alloy can be successfully welded, but only through friction welding.
Forming
When annealed and heat-treated, aluminum alloy 2024 has good machining properties. However, hot forming may not be possible with this aluminum alloy. Applications for 2024 aluminum plates include hydraulic manifolds, fuselage components, shear webs and ribs, and tension members. These plates can range in thickness from 0.25 inches to 6 inches. 2024 aluminum can be used effectively in your applications where structural strength and fatigue resistance are needed.
Comparison of 2024 and 6061
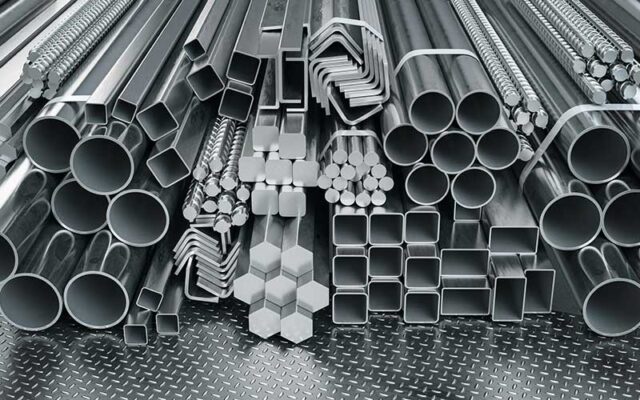
A 6000 series alloy having magnesium as its main alloying element is 6061 aluminum, commonly referred to as “structural aluminum.” Although it has medium to high strength, 2024 is superior in terms of tensile and yield strength. It is less powerful but more versatile. It is easier to weld, more machinable, and more corrosion resistant. It can be used for a variety of things, such as recreational items, plumbing, and building materials. In addition to being employed in wing and fuselage structures, 2024 is also used in homebuilt aircraft more frequently than in commercial or military aircraft.
Comparison of 2024 and 7075
Similar to 2024, the 7075 alloy is widely used in the aerospace sector. This is mostly due to the fact that it is one of the strongest aluminum alloys on the market. It is stronger than 2024 and can reach yield strengths of 73,000 psi and 83,000 psi with precipitation hardening. Applications requiring a high level of stress/strain resistance are ideal for 7075. While 2024 is best suited for applications requiring strong cycle fatigue resistance.